TRAP INSPECTION
The aim of steam trap surveys is to detect problems like steam leaks, low energy efficiency, flooding, inappropriate design or sizing, defective assembly, inadequate discharge temperatures, high back pressure, obstructions, blockages, water hammering, etc.
Usually more than 20% of steam traps leak live steam, what is incompatible with rational use of energy, sustainable growth and fight with Climate Change.
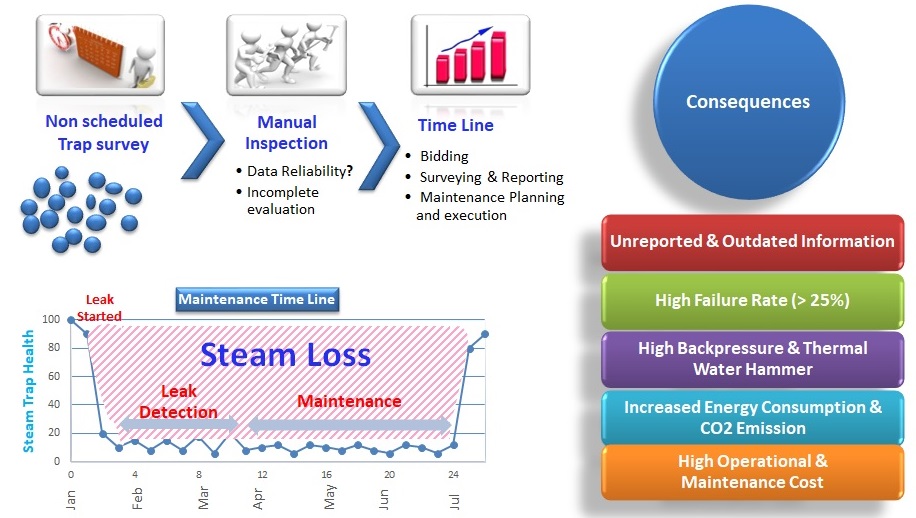
The establishment of an effective program of inspection and predictive, preventive and corrective maintenance considerably reduces all the mentioned incidents and is especially useful to reduce steam leaks, optimize energy efficiency and reduce the emission of greenhouse gases in steam networks. The table shows indicative values of incidents in purge stations in correspondence with the frequency of inspection and maintenance.
Inspection Frequency |
Rate Failure (%) |
24 months | 30 |
18 months | 25 |
12 months | 15 |
6 months | 7 |
3 months | 5 |
1 months | 3 |
Monitored |
<0,2 |
STEAM TRAPS INSPECTION METHODS
The verification of purge stations must check not only the status of all its elements (purge element, blocking valves, bypass,…), but also its suitability and dimensioning for each application, and its energy efficiency. This verification usually requires some experience and a combination of several inspection methods, which are described below:
DIRECT VISUAL INSPECTION
Observing the atmospheric discharge of a purge element requires some experience to distinguish between live steam and expanding steam. The presence of expansion steam in the discharge of a trap is natural and does not imply the existence of a live steam leak. However, the formation of flash steam is greatly reduced in tracing applications due to the partial use of sensible heat from the condensate, a recommended practice to increase energy efficiency, which is currently an essential objective.
The ocular observation of the discharge of a trap to the atmosphere allows to make its diagnosis, although it is difficult to differentiate the live steam from the expansion steam, which can be misleading. The following figures explain the possible situations:

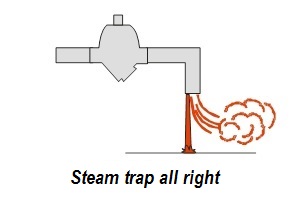
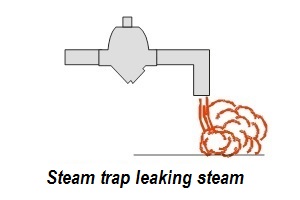
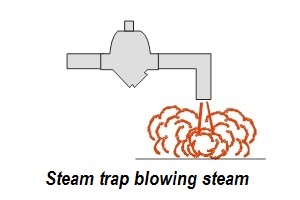
The first figure shows a stream of condensate without flash, indicating that the trap is small and cannot evacuate the entire condensate load. The second figure shows a stream of condensate mixed with flash steam (slightly opaque vapor cloud), indicating trap discharging correctly. The third figure shows a small live steam leak (small transparent steam plume). The fourth figure shows a large steam leak.
When the trap does not discharge to atmosphere but to a manifold, a test valve is required to be able to make a visual inspection. This can be installed upstream or downstream of the trap. If behind the trap there should be a shutoff valve behind the test valve to isolate the trap from the rest of the condensate trap.
The test valve installed in front of the steam trap has the advantage of allowing to verify if what reaches it is live steam or condensation. Indeed, when this valve is opened very slightly, if the drain works correctly, a few drops of water should come out for a moment and immediately steam; on the contrary, if only dry steam comes out, it is a symptom that the steam trap is leaking live steam, since there cannot be expansion steam in front of it. Note that if the test valve is mounted behind the trap it is natural that it will discharge expansion steam, even though the trap is working properly, and this makes correct diagnosis difficult.
In the case of intermittent discharge steam traps (thermodynamic and inverted bucket), the post-trap test valve allows to verify if its operation is intermittent; otherwise the trap leaks steam. If the operation is intermittent, it is very difficult to distinguish whether there is live steam or expansion steam in the discharge, so the diagnosis is not very reliable. This is due to the fact that when the test valve is opened, the actual working conditions of the steam trap are modified, eliminating the back pressure.
In the case of continuous discharge steam traps (buoy), the post-trap test valve always discharges expansion steam, mixed or not with live steam; therefore the visual diagnosis can be imprecise. In fact, it is common and well known that steam traps that do not work well when discharged to a condensate collector, nevertheless work properly when their discharge is diverted to the atmosphere.
VISUAL INSPECTION BY SIGHT GLASS:
Sight Gauge Trap Inspection replaces the test valve with a sight glass placed in the pipeline in front of or behind the trap. There are 3 types of sight glasses:
♦ Simple
♦ Siphonic
♦ Electronics
The simple sight glass is generally installed behind the purge element and only allows to verify the existence of flow through it but it is generally not possible to differentiate between live steam or expansion steam. The siphon sight glass incorporates an internal siphon. It must be installed in front of the purge element and, therefore, it allows to differentiate the state of the fluid (condensate or live steam) because, because it is installed in this position, if steam passage is observed, it can never be expansion steam. In the siphon sight glass, three different situations can be observed as shown in the following figure:
1.- Sight glass totally flooded: It means trap totally flooded due to lack of discharge capacity, obstruction or blockage.
2.- Liquid level flush with the central edge of the siphon: It means correct operation of the steam trap without loss of steam.
3.- Liquid level below central edge of siphon: Means steam leaking trap.
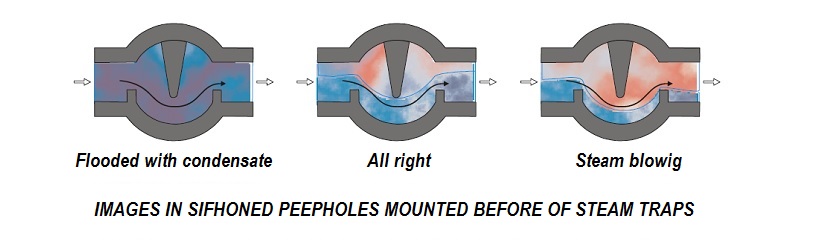
The utility of the sight glasses is limited to low pressures and has the disadvantage of their rapid fouling and loss of transparency due to the progressive deposition of oxide particles on their glass, nullifying their usefulness and increasing the cost of maintenance.
A more sophisticated type of sight glass is the electronic type, which consists of a small container with an internal electrode. When there is condensate, the electrode closes the electrical circuit by conductivity and opens it when there is a vapor leak. The signal is collected by an external measurement equipment that can be connected to the container, but its use is practically null due to its high cost and low reliability, since the electrode is short-circuited when it is covered with an iron oxide (magnetite) film that cancels its function. diagnostic.
INSPECTION BY TIME MEASUREMENT:
This method is only applicable to cyclical steam traps and it measures the time between two consecutive discharges from the trap. A stopwatch is not necessary, it is enough to mentally count 101, 102, 103,… to establish with sufficient validity the duration of the trap cycle in seconds. If there are no cycles, three situations can occur:
1.- Cold trap: out of order or blocked.
2.- Trap flooded and discharge at low temperature: undersized or excessive back pressure).
3.- Steam leak.
If the trap opens cyclically, it must be verified that the duration of its cycle is not excessively short. In thermodynamic disc traps, the duration of the cycle should not be less than 30 s; otherwise, the shorter the cycle, the more deteriorated its internal valve will be and the greater its energy loss.
INSPECTION BY TEMPERATURE MEASUREMENT:
This method, if it is not linked to another, usually leads to errors since it requires knowing more information than is usually available in the field, namely:
♦ Purge type (continuous or intermittent discharge, subcooled discharge or at saturation temperature).
♦ Service (turbine, drip well, process, normal tracing, critical tracing, tank heating …).
♦ Inlet pressure (may vary due to the action of regulating valves or due to consumption variations).
♦ Outlet pressure (it is always an unknown, it is not enough to know the pressure in the general collector but rather the pressure that exists just at the outlet of the steam trap, where there may be strong variations due to the formation of local expansion steam at that point. Its value modifies the temperature drain outlet).
In small flow traps the temperature measurement should generally be discarded since the ultrasonic detection is sufficiently reliable.
ULTRASOUND INSPECTION
It is a fast and fairly reliable method of detecting internal steam leaks. It consists of capturing the ultrasound generated by the passage of steam or gas through an orifice. Indeed, the flow of gas or steam at high speed through a narrowing generates noise in a wide range of frequencies, highlighting the harmonic that corresponds to a narrow range of frequencies around 39 KHz (+/- 2 KHz).
To apply the ultrasound method, it is advisable to know the operation of the purge element, its type of discharge (continuous or cyclical), and select the sensitivity of the instrument corresponding to the vapor pressure; then apply the contact probe firmly on the purge element to read the diagnosis on its LCD screen.
The figure shows the BiTherm LeakTector LT3-EX ultrasound detector, with contact probe, optional directional probe for compressed gas leak detection, discontinuous sensitivity selector and rechargeable battery. This equipment has the intrinsic safety certificate “EX II 1G Ex ia IIC T4 Ga” for use in potentially explosive atmospheres and its high sensitivity allows diagnosing very small vapor leaks.
The reliability of this method depends on how you adjust your measurement scales and user experience. To avoid diagnostic errors and to simplify their use, detectors with a continuous scale selector should be used, since the sensitivity adjustment is critical and depends on the skill of the operator and the results are not always reliable.
Note that the ultrasound method loses reliability when the local back pressure behind the trap is very high and the differential pressure is less than 1 bar (see document ultrasound limitations …).
Note that in case of doubt (for example, in high-flow purge elements where a large amount of flash steam occurs that can generate ultrasound and be interpreted as a live steam leak), several readings should be taken, one on the element itself. purge and another 1 or 2 meters downstream of it. Comparing both measurements, if the detected ultrasound level is similar at all points, the existence of a vapor leak is likely; on the contrary, if the ultrasound is attenuated downstream, it would be produced by the expansion steam, not by the passage of live steam, in which case it should be interpreted as an acceptable state.
INSPECTION BY REMOTE MONOTORING(SmartWatchWeb™)
This is the most reliable method since, unlike the rest, where the situation is only assessed at a given moment, the monitoring takes into account the evolution of the parameters that define the operation of the steam trap over time, identifying substantial changes that they are clear indicators of faults or anomalies.
Monitoring can be total or partial depending on the monitored parameters: ultrasound, temperature, and back pressure. For more information go to Monitoring.
We provide specialized services focused on excellence in energy efficiency of steam networks in the oil refining and petrochemical industry sectors. Our technicians are highly qualified professionals with decades of experience, backed by excellent results.
Visit us
Purgadores de Condensado S.L
Ulises 89, Edifice Bitherm
28043-Madrid(Spain)
Contact us
Phone: +(34) 914 048 087
Fax: + (34) 914 044 875
Email: gestion@bitherm.com