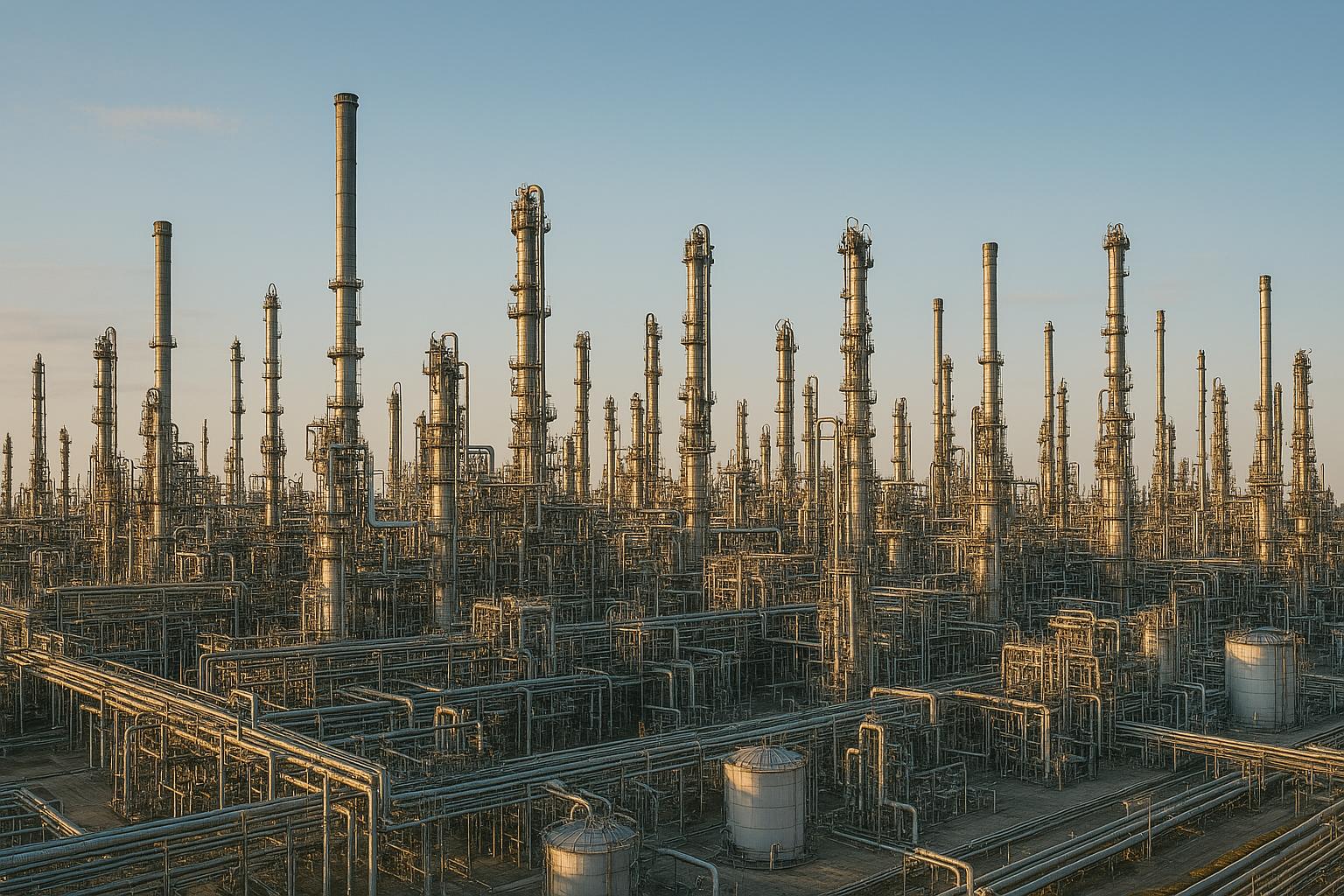
EFFICIENCY PROJECTS IN STEAM TRAPS
Objectives
- Reduce steam consumption more than 15%.
- Keep the trap failure rate below 0.5%.
- Reduce drain inspection and maintenance costs of steam traps.
- Maximize the efficiency of the steam and condensate network.
PHASES
In steam efficiency and steam savings projects in steam traps, 4 phases are distinguished:
Its objective is to quantify as accurately as possible the total value of steam losses due to the condition of the traps, known as the BASE LINE of the project or steam saving potential. There are various evaluation methods, but the most reliable is to apply the Masoneilan formula, approved by the United Nations Agency for CDM projects (Sustainable Development Mechanism – Kyoto Protocol).
It consists of analyzing the various options, in terms of the type of trap, available monitoring technologies and architectures, reliability, future maintenance cost, etc., associated with the development of the project, and assessing each one of them to obtain a comparative cost-benefit study that allows determining the viability and profitability of each option, and if applicable, selecting the most advantageous option.
This phase consists of carrying out the detailed engineering and subsequently executing all the construction tasks and installation works of the elements selected in the previous phase. It also includes the areas of testing, start-up, training of personnel, …, corresponding to the execution of the project. Emphasize that monitoring is necessary, but not sufficient to achieve the project objectives.
This is the most important phase and consists of analyzing the information obtained by the monitoring system and immediately taking the necessary actions to correct steam leaks and incidents detected by the system, which we call “INTENSIVE MAINTENANCE”. The urgency in applying these preventive and corrective actions is essential to achieve the project objectives.
Featured references
IBERIAN LUBE OILS COMPANY, S.A. (ILBOC) is a joint venture (JV) between SK LUBRICANTS (South Korea, world leader in the lubricating base oils market) and REPSOL PETROLEO (the leading refining company in Spain). ILBOC started production by becoming the largest new generation lubricating base oil production facility in Europe.
This large-scale ISA100 wireless steam trap and valve monitoring project has reduced costs associated with sensor installation and simplified the process of monitoring 904 items (possibly the world’s largest current ISA100 installation) by combining into one single management platform multiple applications:
- Fight against climate change. Monitoring of steam leaks and energy efficiency in steam traps.
- Security. Monitoring of leaks of dangerous gases in safety valves.
- Prevention and Health of Personnel. Detection of toxic gases (H2S) in the environment.
- Catastrophic Risk Prevention. Detection of explosive gases (hydrocarbons) in the environment.
This refinery has been a pioneer in the world in implementing a project to save steam using intelligent traps Bitherm SmartWatchWeb (year 2001). Once the excellent results have been verified, this technology has been implemented in multiple Process Units. One of the greatest successes of these projects was evident in the Vacuum Desulfurization and Distillation Units, where steam installations are very critical due to the processing of solidifiable or high viscosity products. In them, the enormous usefulness of the Bitherm SmartWatchWeb intelligent steam traps has been proven, not only due to the substantial steam savings achieved, but also due to the improvement in operating conditions and the significant increase in reliability that they have meant for the steam network in these facilities. Process Units (see reference published by REPSOL).
These projects have been developed by PURGADORES DE CONDENSADO SL (Group BITHERM) in the turnkey mode, including the implementation of the Intensive Maintenance Methodology in the following Process Units:
♦ Unity of Desulfurization 639
♦ Unity of Desulfurization 644
♦ Unity of Desulfurization 661
♦ Unity of Vacuum Distillation 624
♦ Unity of Coke 641
♦ Unity of Olefins 802
♦ Unity of Benzene 810
♦ Unity of Lubricants 701
♦ Unity of Lubricants 710
♦ Unity of Lubricants 720
♦ Unity of Lubricants 721
♦ Unity of Lubricants 731
The first of the projects to save steam using Bitherm SmartWatchWeb smart traps was carried out in 2010. Since then we have carried out several similar projects, all of them with excellent results of increased reliability, reduced inspection and maintenance costs, improvement in operating conditions. and high steam savings (see reference published on its own website). The results have also been published in his magazine “Gaztelu Berri” (see article).
These projects have been developed by BITHERM turnkey, including the implementation of the Intensive Maintenance methodology in the following Process Units:
♦ Unity of de Asphalts
♦ Unity of Desulfurization SR3
♦ Unity of Desulfurization SR4
♦ Unity of Desulfurization SR5
♦ Unity of Desulfurization SR6
♦ Unity of Vacuum Distillation V3
♦ Unity of Coke CK6
At the same time, the use of BiTherm Magnus multi-element traps has improved the operation and efficiency of the steam in tanks and heat exchangers in their facilities. (see reference).
The first project to save steam using Bitherm SmartWatchWeb smart traps was carried out at this refinery in 2006. Highlight the excellent results of increased reliability and efficiency, reduced inspection and maintenance costs, improved operating conditions and high steam savings. These projects have been developed turnkey and implementing the Intensive Maintenance Methodology in the following Process Units. (see reference):
♦ Unity 751 Desphalted 2
♦ Unity 752 Furfural 3
♦ Unity 753 Dewaxed 3
♦ Unity 754 Vacuum 4
♦ Unity de Desulfurization 685
Since 2003, this refinery has carried out several steam saving projects using Bitherm SmartWatchWeb intelligent traps. Highlight the excellent results of increased reliability and efficiency, reduction of inspection and maintenance costs, improvement in operating conditions and high steam savings. These projects have been developed by the Bitherm Group turnkey, including the application of the Intensive Maintenance Methodology in the following Process Units:
♦ Unity 1303 – Coke
♦ Unity 1301 – Empty 2
♦ Unity 1220 – PRA 3
♦ Unity 1314 – PRA 4
♦ Unity 1201 – Crude 1
♦ Unity 1203 – Empty 1
♦ Unity 1204 – Platformed 1
♦ Unity 1206 – Gases 1
The first project to save steam using Bitherm SmartWatchWeb smart traps was carried out at this refinery in 2013. Since then, several projects of the same type have been carried out, all of them with very satisfactory results. The failure rate in steam traps has been reduced to practically zero, improving the reliability of the facilities. These projects have been developed turnkey, including the implementation of the Intensive Maintenance methodology in the following Process Units:
♦ 2 Desulfurization Units
♦ Unity Area 7
♦ Collector and tank areas
In 2017, this refinery carried out its first steam saving project using Bitherm SmartWatchWeb smart traps. The project has been developed in a turnkey mode by BITHERM GROUP in collaboration with the local Saudi company TANAJIB.
Highlight the excellent results of increased reliability and efficiency, reduction of inspection and maintenance costs, improvement in operating conditions and high steam savings. Highlight the enormous interest of SAUDI ARAMCO in implementing new technologies for energy optimization and reduction of atmospheric emissions and / or pollutants in its facilities, in accordance with its policy of sustainable growth and environmental protection.
This refinery is in the construction phase. The Bitherm Group in collaboration with the local Saudi company TANAJIB has supplied over 6,000 Bitherm SmartWatchWeb monitored smart traps since 2016 for various Process Units.
Highlight the enormous interest of SAUDI ARAMCO in implementing new technologies for energy optimization and reduction of atmospheric emissions and / or pollutants in its facilities, in accordance with its policy of sustainable growth and environmental protection.
Limitations of ultrasounds
Ultrasonic detection has become a highly valuable tool for predictive maintenance, for detecting gas or vapor leaks in valves. However, it is necessary to know its limitations when it is applied to the detection of steam leaks in steam traps and steam traps, where the discharge of condensate generates expansion steam that can be erroneously interpreted as a live steam leak.
We provide specialized services focused on excellence in energy efficiency of steam networks in the oil refining and petrochemical industry sectors. Our technicians are highly qualified professionals with decades of experience, backed by excellent results.
Visit us
Purgadores de Condensado S.L
Ulises 89, Edifice Bitherm
28043-Madrid(Spain)
Contact us
Phone: +(34) 914 048 087
Fax: + (34) 914 044 875
Email: gestion@bitherm.com